Plastic Molds are used to create a variety of products. These products range from packaging and electronic components to machine tools and household items. Contact American Plastic Molds now!
Unlike production tools that are made from hardened steel, short-run injection molds use aluminum, which is less expensive. These tools are also more flexible and can be produced in much shorter turnaround times.
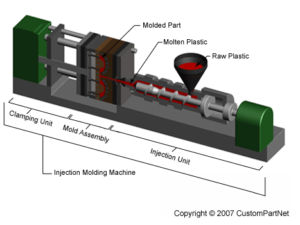
Rotational molding is a process that creates hollow, one-piece construction products. Unlike many other rapid, high-pressure processes, this method relies on a series of heating and cooling cycles to form the product. It’s also slow compared to other high-speed processes, with most machines spinning molds at around eight rotations per minute.
The process begins with loading a measured amount of powdered resin into a hollow, bi-axially rotating mold coated in a special mold release agent. The resin is then heated while being slowly rotated until it’s molten and covers the entire mold. The mold is then cooled with air or water, depending on the polymer resin used.
During the cooling process, it’s important to monitor the temperature inside the mold. If the temperature rises too rapidly, the molten plastic could degrade or weaken. This would result in a weakened impact strength, and it may even cause the part to warp.
Once the molten resin is completely cooled, the operator can remove it from the mold. This is an important step because it’s the only way to ensure a smooth finish on the finished product. It’s also necessary to ensure that the molded material doesn’t have any voids or air pockets.
The most common polymer for rotomolding is polyethylene, as it’s easy to work with in its molten state and has good thermal stability. While other materials can be used in rotational molding, they’re typically only utilized in a small percentage of production due to their higher costs. Some materials also have a hard time converting to a fine, powdered form, making them unsuitable for this type of processing. Other limitations of the rotomolding process include a long cycle time, limited material options, low repeatability and short tool life. This is because the tooling needed for this process consists of soft metals that need to be replaced or repaired after 3,000 cycles. In addition, the rotational molding process is labor intensive. This can lead to a high cost of operation for producers. This is particularly true when the mold is designed with features that require complex geometry and/or multiple ribs.
Injection Moulding
Plastic injection molding is a very versatile process which can produce a huge variety of parts. It is highly repeatable, leading to a high quality of product. It’s environmentally friendly and requires little to no post-production work. Its initial cost is quite expensive, making it best suited for those who need a large volume of products.
The basic process is simple: raw material, usually in the form of pellets, is melted under high pressure using heat and then injected into the mould via a pipe called a sprue. The molten material then cools, solidifying into the desired shape of the part. Once cooled, the part is clamped and ejected from the mold.
Injection molding is used to manufacture many different types of products, including medical items like syringes, gloves and IV tubes as well as consumer plastics such as mobile phone cases, bottle caps and toys. It is also used in a wide range of other industries, from construction to electronics.
It is important to plan the design of an injection molded part carefully. This can help reduce the risk of common defects such as warping, sink marks and short shots. For example, if your design has areas of varying wall thickness, try to make them as uniform as possible by using chamfers or fillets. Thick sections are more prone to sinking and warping than thinner ones, so if possible, try to make thick sections hollow.
Another key factor in reducing the risk of these problems is draft angle. This is a taper applied to the vertical surfaces of the mould, helping the molten plastic release more easily once it has cooled. It is recommended that you use a minimum of 2 degrees, and larger on taller features.
Injection molded parts often require holes for screw threads and other fastening and assembly hardware. These can be modeled directly into the part using a technique known as in-mould labelling, which is extremely efficient. Alternatively, threaded inserts can be inserted during the injection cycle, or a boss can be added to the part for attachment. The latter is a cylindrical projection with holes that can be designed for screws or other types of fastening. Undercuts, which occur when a feature extends into an area that isn’t sealed by the mould, can be eliminated by clever redesign or by using a shut-off.
Extrusion Moulding
The extrusion molding process is ideal for producing long, continuous plastic parts. This type of molding is often used to produce items such as weather stripping, windshield wiper blades, pipes, and window frames. The extrusion process involves a plastic or rubber polymer being heated above its recrystallization temperature and then forced through a machined metal die to form the desired shape. The resulting product is then cooled to set the material.
Unlike injection molding, which has more design flexibility, extrusion is best for products that require consistent, uniform cross sections. It’s also suitable for products with simple, straight shapes, such as piping and tubing. Extrusion is less suited for manufacturing three-dimensional products that have complex shapes or details, but it’s still an excellent option for products such as plastic drinking straws and fuel lines inside automotive engines.
Extrusion molds typically have lower tooling costs than other types of plastic molding. It’s a cost-efficient production method that’s particularly beneficial for longer production runs of the same part. In addition, the extrusion process can be a more environmentally sustainable way to manufacture plastics since it minimizes the use of virgin plastics.
Tolerance levels for extrusions are not as stringent as those of injection molding, but the manufacturing process can still be optimized for quality and efficiency. Optimizing the cooling rate, material flow, and process parameters can improve quality, increase production speeds, and reduce production times.
The benefits of plastic extrusions include their versatility and durability. They are available in a variety of colors and finishes, and they can be made from many different engineering thermoplastics or polymer blends, including high-performance materials such as PEEK. Additionally, they can be manufactured in both solid and hollow forms.
Tolerances for plastic extrusions are less precise than those of injection molding, but the manufacturing process is still highly efficient and can be used to produce a wide range of products. Process efficiency improvements, such as cycle time and material usage optimization, real-time monitoring, and automated quality control, can increase production speed and maintain consistency. Quick mold change systems, work cell flexibility, and setup optimization can further reduce production time and labor costs while improving productivity.
Sheet Moulding
Sheet Molding Compound, or SMC, is a pre-made composite material that combines fiberglass with resin and fillers. This material is used for large-scale production, and it offers a cost-effective and reduced-waste alternative to other composites, such as bulk molding compound (BMC). This process can be utilized with both compression and injection moulding, but it’s ideally suited for high-volume applications.
SMC is made up of a blend of polymer resin, inert fillers (like calcium carbonate, talc or wollastonite), glass fiber reinforcement, catalysts, pigments, stabilizers, release agents and thickeners. It is a thermosetting compound with excellent mechanical properties, exhibiting high strength and rigidity. It also has good electrical performance and is resistant to corrosion in various chemical environments.
The SMC production process is straightforward and quick, allowing manufacturers to produce parts in as little as a minute per piece. The material is formed into a shape with a compression molding press, which heats and compresses the SMC to form it into an exacting shape. The process can handle a wide range of geometries, making it ideal for the manufacture of vehicle body panels and components.
In the automotive industry, SMC is commonly used to produce door assemblies, roof panels, spoilers, fenders and bumpers. The lightweight nature of this material makes it ideal for reducing the weight of vehicles, while still offering an impressive level of protection in the event of an accident. Moreover, SMC is capable of achieving class “A” surface finishes without the need for a secondary painting process.
SMC is also a great choice for the production of high-quality interior panels, as it is highly durable and can withstand harsh environmental conditions. This material is also highly customizable, with the ability to incorporate ribs and bosses into the final product. In addition, it is able to flow during the moulding process, which allows for complex shapes and a high degree of precision in the finished product.